The Importance of Preventive Maintenance in Material Handling Systems
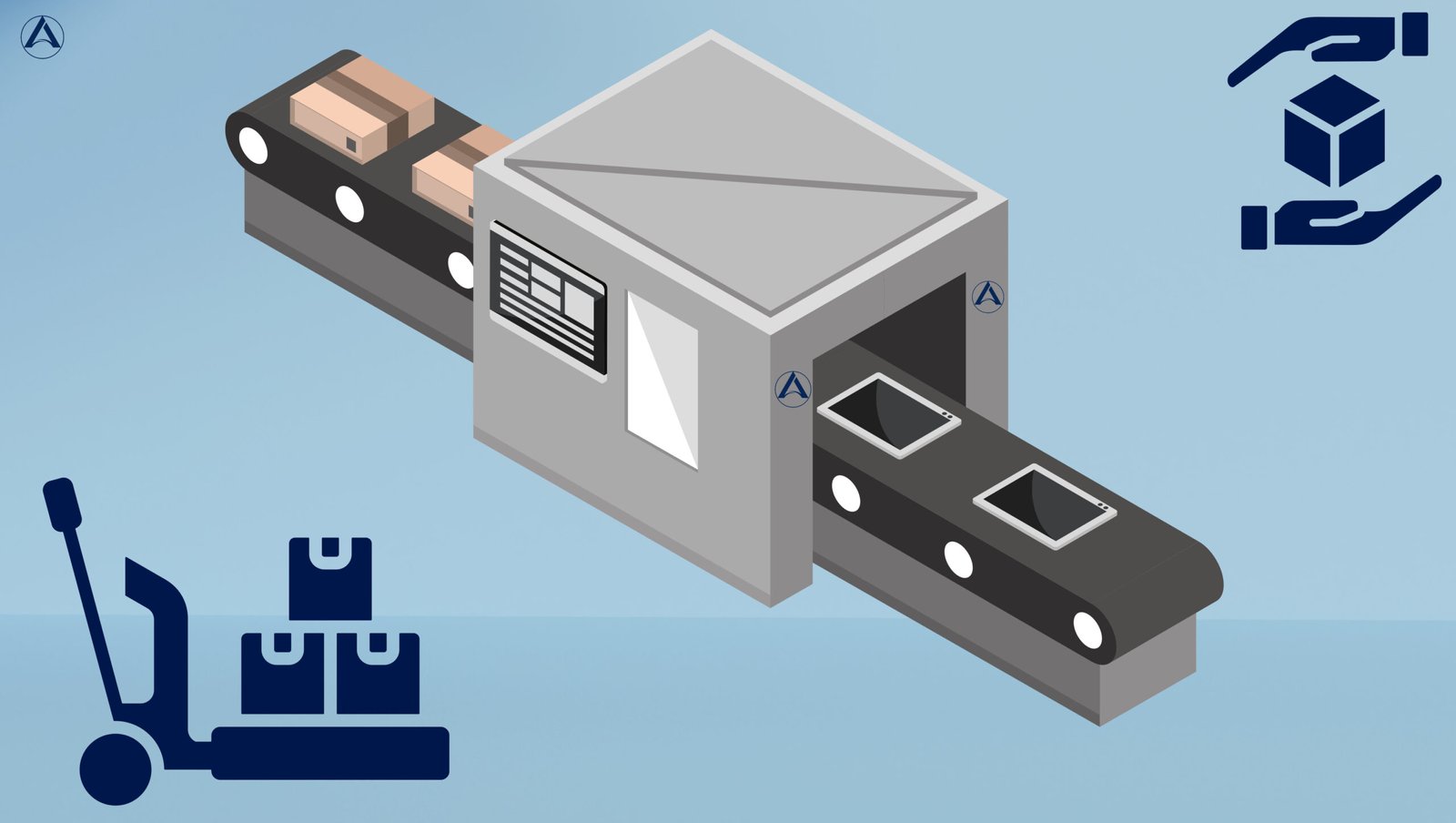
Material handling systems are the backbone of industries such as manufacturing, logistics, and warehousing. These systems—ranging from automated conveyors to robotic arms—ensure the smooth movement of goods and materials. However, to keep them operating at peak efficiency, preventive maintenance is critical.
What is Preventive Maintenance?
Preventive maintenance involves scheduled inspections, adjustments, and repairs to prevent unexpected breakdowns. Unlike reactive maintenance, which deals with issues after they occur, preventive maintenance focuses on minimizing downtime and extending the equipment’s lifespan.
Benefits of Preventive Maintenance
- Enhanced Equipment Longevity
Regular maintenance ensures that components like motors, belts, and sensors in material handling systems are kept in optimal condition. By addressing wear and tear early, companies can avoid costly replacements. - Minimized Downtime
Unplanned equipment failures can disrupt operations and lead to significant financial losses. Preventive maintenance reduces the likelihood of such disruptions, ensuring continuous workflow. - Improved Safety
Faulty equipment can pose safety risks to workers. Regular maintenance helps identify potential hazards, such as frayed conveyor belts or malfunctioning robotic arms, mitigating risks. - Optimized Efficiency
Well-maintained systems operate smoothly, consuming less energy and increasing productivity. For instance, properly aligned conveyors reduce resistance, resulting in lower energy costs.
Key Steps in Preventive Maintenance
- Regular Inspections
Conduct thorough inspections of all components, including motors, rollers, chains, and sensors. Look for signs of wear, misalignment, or corrosion. - Lubrication and Cleaning
Keep moving parts well-lubricated to reduce friction. Clean components to prevent debris buildup that can hinder performance. - Software Updates
For automated systems, ensure that control software is regularly updated. Outdated software can cause inefficiencies and increase the risk of errors. - Component Replacement
Replace parts like belts, sprockets, or bearings at regular intervals to prevent sudden failures.
The Role of IoT in Predictive Maintenance
The integration of Internet of Things (IoT) technology takes preventive maintenance to the next level. IoT-enabled sensors collect real-time data on equipment performance, such as vibration levels, temperature, and operational hours. This data is analyzed to predict when maintenance is required, enabling proactive scheduling.
Conclusion
Preventive maintenance is an essential strategy for businesses that rely on material handling systems. By investing in regular upkeep and leveraging advanced technologies like IoT, companies can reduce costs, improve efficiency, and maintain a safer working environment. A well-maintained system not only supports current operations but also positions businesses for long-term success in a competitive market.
Let’s Build the Future Together
At Agamus, we empower businesses with cutting-edge technology solutions tailored to your unique needs. Whether it’s software development, cloud computing, or cybersecurity, we’re here to drive your success. Contact us today to turn your ideas into reality!